Adhering to the back panel of smart devices
The primary task of the back panel is to protect the integrated components inside the device casing. New technological advancements, such as 5G or wireless charging, also impact the construction of the back panel. Industrial adhesive tape meets the requirements of these new technologies.
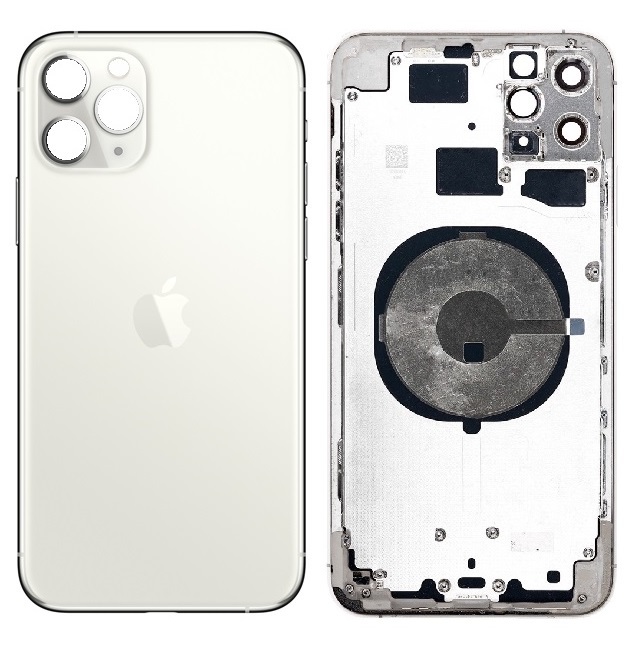
High adhesive strength is a fundamental requirement for back panel attachment solutions. Since the back panel must protect the internal components, industrial adhesive tape must have the ability to resist impact, chemicals, and provide good sealing to prevent damage from external forces or particles (dust, sand) and liquids (water, chemicals) entering the device. For curved designs or foldable devices, good fold resistance characteristics are also crucial.
Adhesive tape characteristics:
- Ultra-thin.
- Transparent bonding.
- Flexible, meets all product design requirements.
- Easy to apply, suitable for production lines, automation.
- Sealing capability.
- Impact resistant.
- Chemical resistant.
- Can be repositioned.
Applications:
- Adhering to the back panel of smartphones.
- Adhering to the back panel of smartwatches.
- Adhering to the back panel of tablets.
Bonding smart device batteries
The role of battery attachment plays a pivotal role in the current development of new smart devices: battery performance will enhance the device’s efficiency, while designs must remain thin to achieve sleek, modern aesthetics for mobile devices or to accommodate entirely new designs like foldable devices.
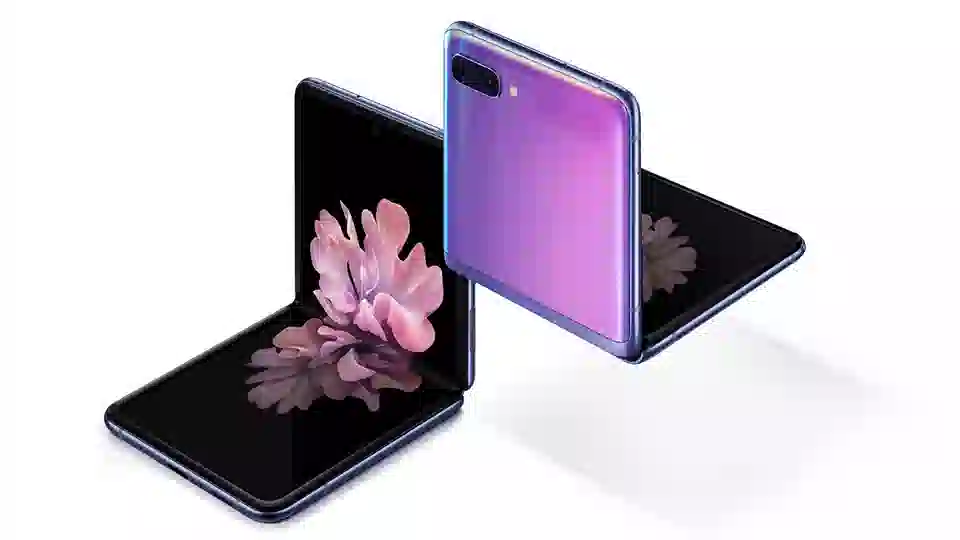
European regulations and increasing customer concern for environmental solutions are driving manufacturers to ensure the recyclability of devices, making removable batteries a necessity. Suitable industrial adhesive tape solutions can overcome these challenges and open up entirely new design possibilities.
Requirements for adhesive tape:
High adhesive strength, durability over time combined with shock reduction and slip resistance are essential to avoid the risk of battery damage. Depending on the battery mounting method, the tape must also be removable to ensure that the battery can be easily and safely detached. The availability of various thicknesses of adhesive tape provides manufacturers with greater freedom and flexibility in battery design.
Adhesive tape characteristics:
- Shock resistance.
- Impact resistance.
- Removability after application.
- Slip resistance, displacement resistance.
Methods of battery attachment:
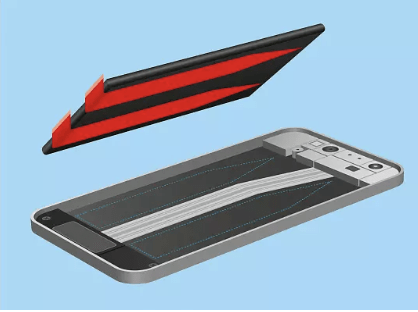
Tension bonding: The battery with a cut-out mold is attached to the casing. By tension bonding, the battery can be easily removed without any excess residue. High tear resistance and low removal force are crucial factors for this method, allowing for complex battery designs.
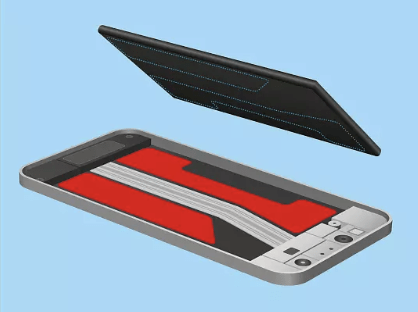
Solvent removal: Tape is adhered to the battery, then attached to the casing. The key to this method is the initial high bonding performance of the tape, but the bonding strength decreases significantly after solvent use, allowing for easy battery removal. This method enables thin designs.
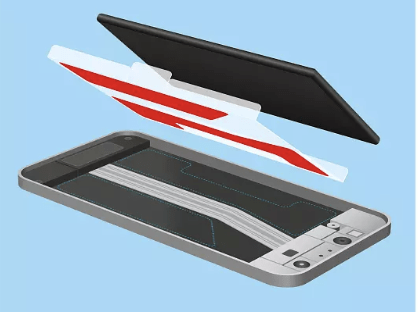
Re-encapsulation bonding: The battery is encapsulated and bonded with a PET film. This film is then bonded to the casing using high-performance adhesive tape. If needed, the battery can be easily removed from the encapsulation and the casing. Thinner tape is often required due to multi-layer designs.
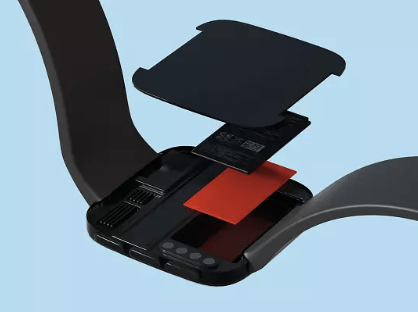
Permanent bonding: Along with efficiency, high bonding strength and good impact resistance are important characteristics for permanent battery attachment. This method allows for very thin designs. On the other hand, the battery removal process is relatively complex, as low or high temperatures are required to break the bond.
Glass & screen assembly
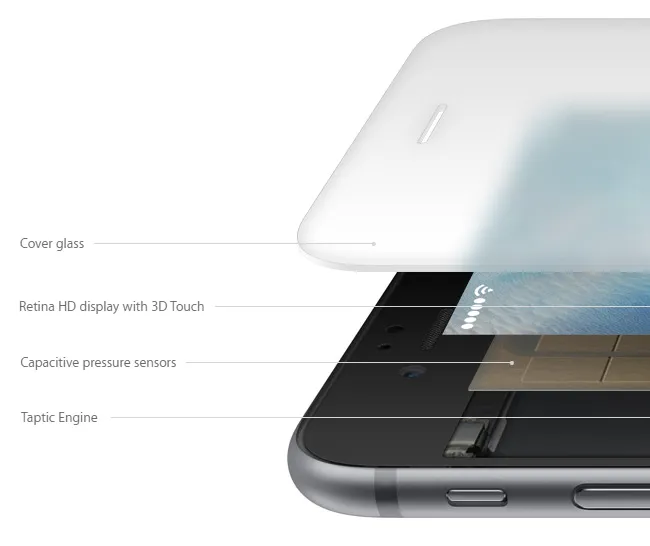
Glass is one of the largest and most distinctive components of mobile devices, as it appears in cameras & touch screens, defining the overall design and serving as the interaction surface with users. Moreover, screens are highly susceptible to damage due to daily exposure to external impacts. Adhesive tape solutions can help overcome these emerging challenges.
Requirements for adhesive tape
- Impact resistance: This is a crucial requirement as mobile devices frequently encounter mechanical shocks such as drops, impacts, or vibrations. The tape must have the ability to reduce these impacts to protect the screen.
- Sealing capability: Highly important to prevent dust, water, or other substances from infiltrating and damaging the device’s interior.
- Resistance to chemical substances: Examples include sweat or sunscreen, especially for wearable devices.
- Recyclable solutions: Easily allow for repair and recycling processes, saving costs and ensuring safety.
A fundamental condition for glass assembly solutions is a very strong bonding performance to prevent the lens & screen from detaching from the casing. This must also be ensured in harsh environmental conditions such as high temperature or humidity.
Contact Us
Hitta specializes in providing industrial adhesive tape for various industrial and commercial sectors. Contact us for the most cost-effective and efficient solution advice.
- ☎️ Hotline: 090.8611.011 (Mr. Dương).
- ✉️ Email: hittajsc@hitta.vn
Tham khảo sản phẩm:
-
Bow Tape 110 (0.11 mm)
-
Bow Tape 110QJB (0.16 mm)
-
Acrylic Foam Tape Bow Tape 723G (2.3 mm)
-
Acrylic Foam Tape Bow Tape 730W (3.0 mm)
-
Acrylic Foam tape with LSE coating – Bow Tape 708GLM (0.8 mm)
-
Bow Tape PE foam Tape 398A (0.8 mm)
-
Bow Tape PE foam tape 398EW (1.0 mm)
-
Bow Tape 391W (1.6 mm)
-
Bow Tape 300NHK
-
Acrylic Foam Tape – Bow Tape 711BH
-
Acrylic Foam Tape – Bow Tape 715B (1.5 mm)
-
Bow Tape 3510PP (0.1 mm)
-
Bow Tape 550 (0.17 mm)
-
Acrylic Foam Tape – Bow Tape 7025THH
-
Bow Tape 1750L (0.05 mm)
-
Bow Tape 590 (0.09 mm)
-
Bow Tape 710SF (1.0 mm)
-
Bow Tape 3510B
-
Bow Tape 3505B
-
Bow Tape 716GS
-
Bow Tape 706BH (0. 6mm)
-
Transparent Reinforcement Tape Bow Tape 710T (thickness 1.0 mm) Self-Adhesive
-
Bow Tape 110QJ (0.16 mm)
-
Bow Tape 704WE (0.4 mm)
-
Bow Tape 706BH (0.6 mm)
-
Bow Tape 708GSX (0.8 mm)
-
Acrylic Foam Tape Bow Tape 711G (1.1mm)