Bonding & assembling teak wood panels for yacht and ship decks requires high aesthetic appeal, resilience to harsh environments, and high sealing capability. Hitta’s industrial adhesive solution optimizes costs, streamlines assembly processes, and enhances durability for wooden decks.
Wood Quality
Teak wood is a preferred choice in the shipbuilding and yacht industry due to its resistance to wind, weather, and pests. Therefore, in this article, Hitta will use the conditions and quality of teak wood as a general template for the process of decking for ships and yachts.
In both dry and wet conditions, teak wood ensures anti-slip properties and protects the deck against weather effects, providing a durable deck surface. Because of these characteristics, selecting the method of bonding teak wood panels requires precise requirements and similar properties.
Only teak wood with vertical annual rings (heartwood) should be used. The core moisture content of the wood must be between 9% and 12%. When the moisture content in the wood is too high during the construction of teak wood decking, drying the wood later will cause the wood to shrink, leading to permanent deformation of sealants and adhesives. This will adversely affect the durability of the entire wooden deck. Ideally, the moisture content of the wood during the deck construction process should be equivalent to the moisture content of the wood during construction.
Working under appropriate conditions during adhesive application and filling is a basic requirement for good results. The air temperature must be between +5°C and +35°C. During the panel bonding process, the relative humidity must be between 40% and 75%. Working indoors or in air-conditioned areas provides better quality assurance compared to outdoor work. During construction and while waiting for the sealants and adhesives to cure, the deck must be protected from direct sunlight and rain, as uncontrollable impacts may occur.
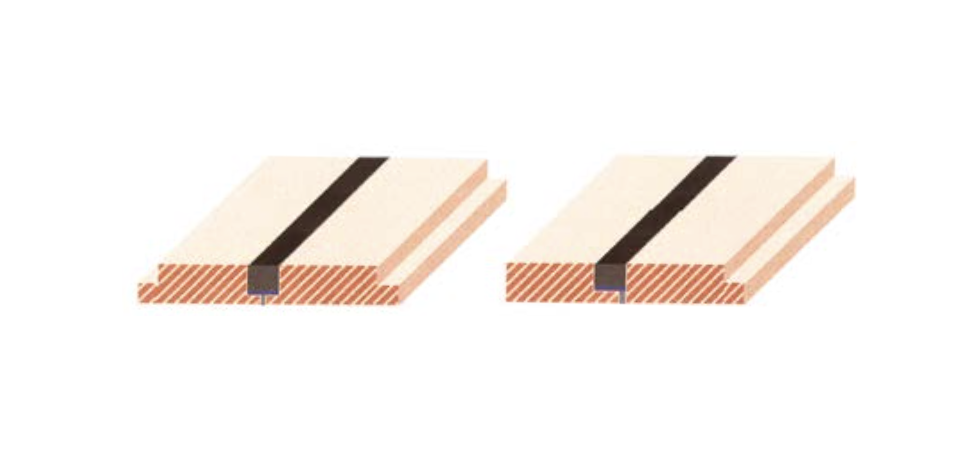
The wooden panels for decking come in different cross-sectional shapes: T-shape and L-shape (see the diagram above). The T-shape cross-section, with the separation of lines in the middle, is preferred over the L-shape cross-section. Movements due to thermal and environmental conditions will be compensated for optimally by adhesives and sealants. When using the L-shape profile, it’s important that the adhesive fits snugly with the joints.
Recommended Products
Surface Preparation Procedure
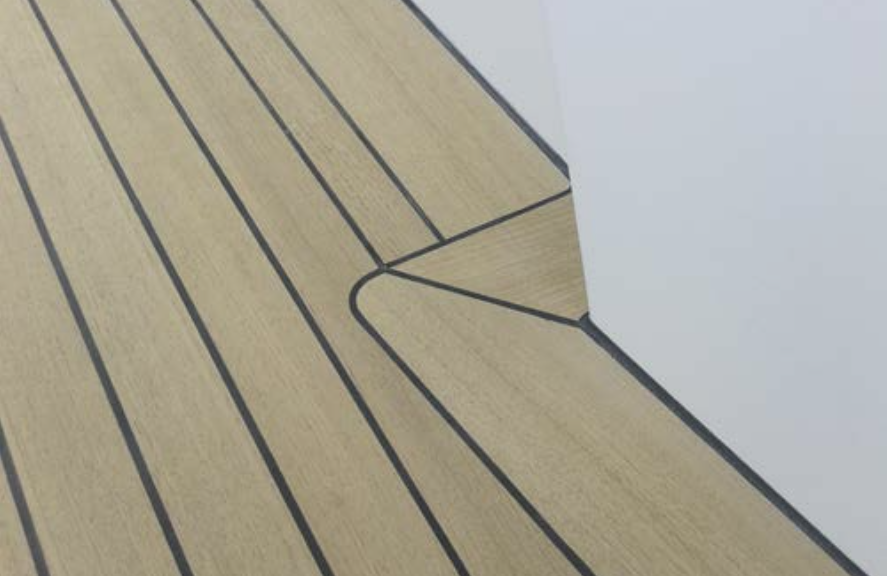
Wooden Floor
All wooden surfaces to be in contact with adhesive and filler need to be treated beforehand with a specialized solution. Application should be done with a suitable roller or brush to create a thin but continuous coating.
Drying time: minimum 1 hour, maximum 6 hours.
All old surfaces must be sanded with 80 or 100 grit sandpaper and thoroughly vacuumed with a high-power vacuum cleaner to remove dust particles.
New Wooden Floor:
All areas to be glued must be cleaned.
Apply adhesive/sealant to the surface using a clean cloth (colorless, lint-free).
Drying time: minimum 5 minutes, maximum 6 hours.
Old Wooden Floor:
Remove all old layers of construction and clean with a specialized cleaning solution.
The overall surface should be lightly sanded with 80 or 100 grit sandpaper.
The overall surface must be thoroughly vacuumed with a high-power vacuum cleaner to remove dust particles that may adversely affect adhesion.
Apply adhesive/sealant to the surface using a clean cloth (colorless, lint-free).
Drying time: minimum 5 minutes, maximum 6 hours.
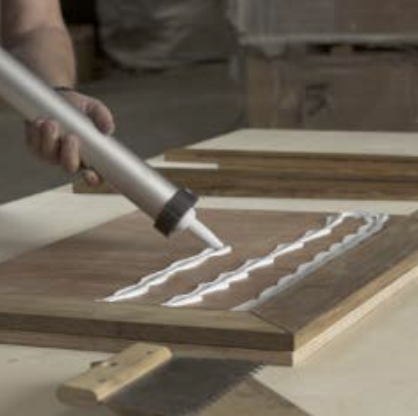
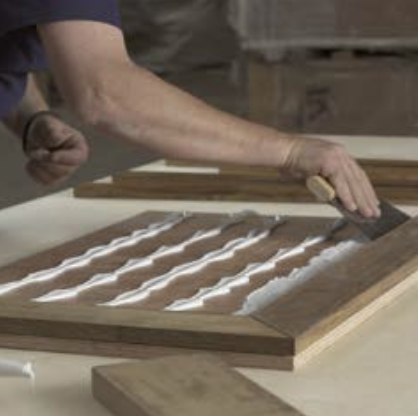
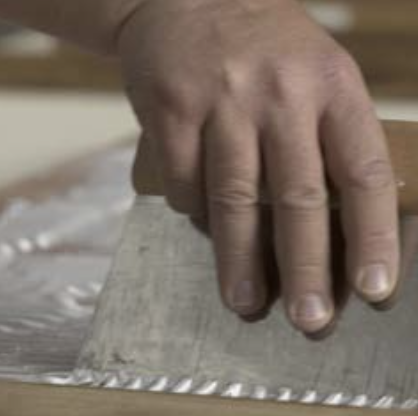
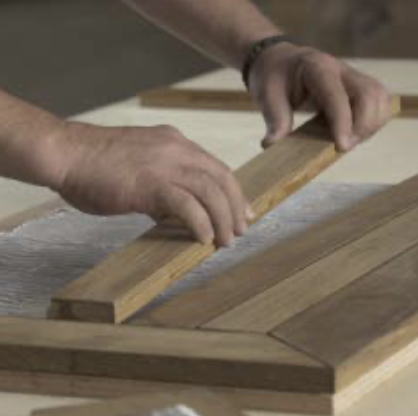
Steel or Aluminum Floor
There are various surface coatings and surface grinding machines available for use on steel and aluminum floors. Due to the wide range of these products, it’s not possible to provide a general recommendation for application. Hitta advises conducting adhesion and durability tests with the products or contacting us for guidance.
Preparing for the joints
- Completely remove old adhesive and any remaining materials.
- Joints must be clean, dry, and free of dust. Do not clean with compressed air as it may contain oil. Instead, use an industrial vacuum cleaner.
- Use a specialized cleaning solution.
- Apply the cleaning solution with a brush continuously along the joint edges, creating a thin layer by brushing multiple times onto the joint (see the diagram below).
- Drying time: minimum 1 hour, maximum 24 hours.
- Temperature should be between +5°C to +35°C.
- Maximum relative humidity is 75%.
- Wood floors will contract and expand due to changing environmental conditions. Joint grooves on the planks will adapt to these movements without losing adhesion.
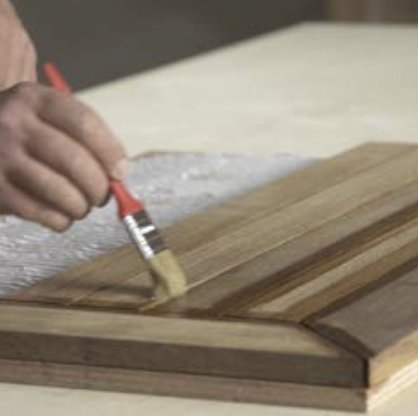
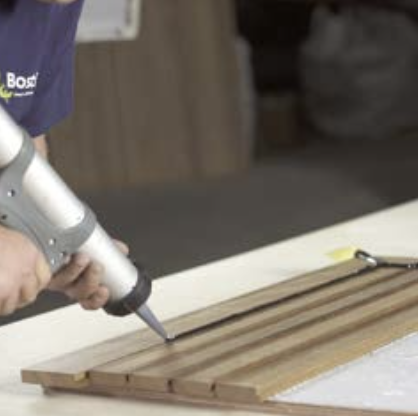

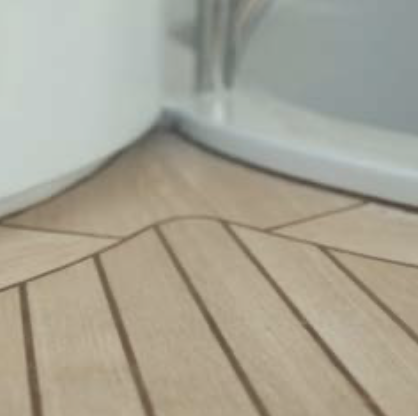
Bonding Wood Panels
- Apply adhesive to the pre-treated and spread-out joint surface using a trowel (5×6 mm teeth). The expected usage rate is approximately 1500-2000 ml/m2, depending on the height difference of the joint.
- The mixture should be spread over the entire surface of the joint to protect it from moisture ingress. Do not apply more adhesive than can be handled within the product’s curing time.
- Apply a cleaning solution to the surfaces of the teak wood panels to be bonded (waiting for the cleaning solution to dry), place the wood panel into the adhesive, and use light pressure to ensure that the wood surface is fully wetted.
- Secure the wood panel using clamps for at least 24 hours. After 24 hours, the clamps can be removed. Any remaining uncured adhesive can be removed using chemicals or mechanical means.
Joint Filling
The strongest joint is achieved when using the correct size. Refer to the following table for the correct sizes:
The width of the wood plank(mm) | The minimum width of the joint (mm) | The minimum depth of the joint (mm) |
35 | 4 | 6 |
45 | 4 | 6 |
60 | 5 | 6 |
90 | 6 | 7 |
95 | 6 | 8 |
120 | 16 | 10 |
The minimum joint size ensures that deformations can occur within a reasonable range when the temperature and/or humidity in the wood change.
During the joint filling process, the seams must:
- Be protected from direct sunlight and rain.
- Have a temperature ranging from +5°C to +35°C, and relative humidity from 40% to 75%.
- Cut the sealant nozzle to match the width of the joint.
- The joints must be filled from bottom to top to prevent air gaps in the joint. The nozzle should be placed at the bottom of the joint, and the gun held at a 60° to 80° angle. Pull the nozzle steadily through the joint on the board with a surplus of 10% to 20%.
- After 3 to 7 days (depending on temperature and relative humidity), the wood boards can be sanded.
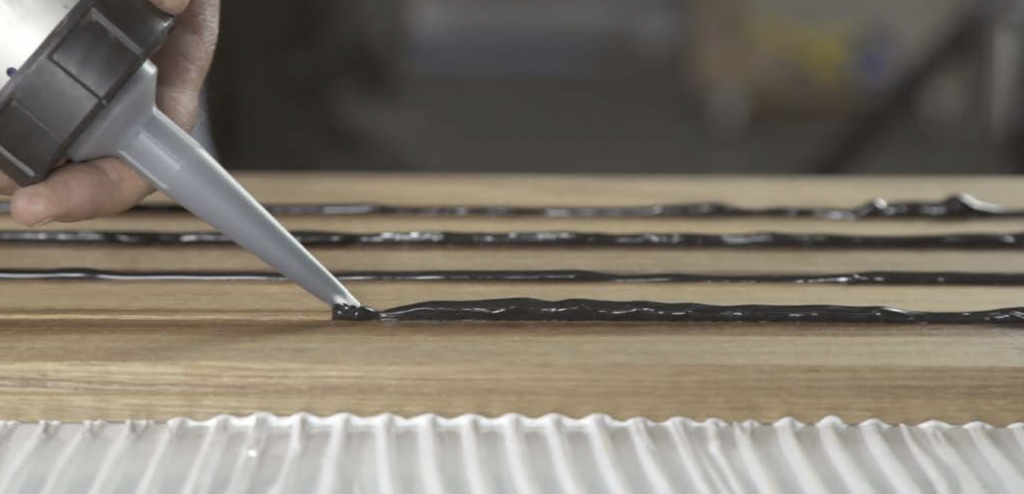
Final Finishing
Before sanding, remove any excess material. Sanding the seam should be done in at least two steps, first with 80-grit sandpaper in the direction parallel to the seams. The second step should be carried out with at least 120-grit sandpaper.
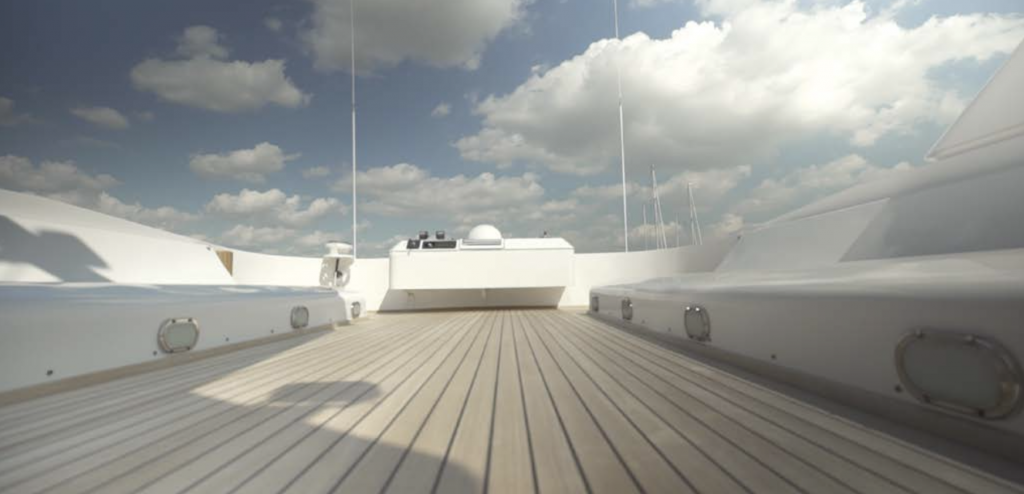
Contact information
Hitta specializes in providing various types of adhesives and tapes for both industrial and commercial sectors. Contact us for advice on the most efficient solutions at the lowest cost.
- ☎️ Hotline: 090.8611.011 (Mr. Dương).
- ✉️ Email: hittajsc@hitta.vn